clay cracks
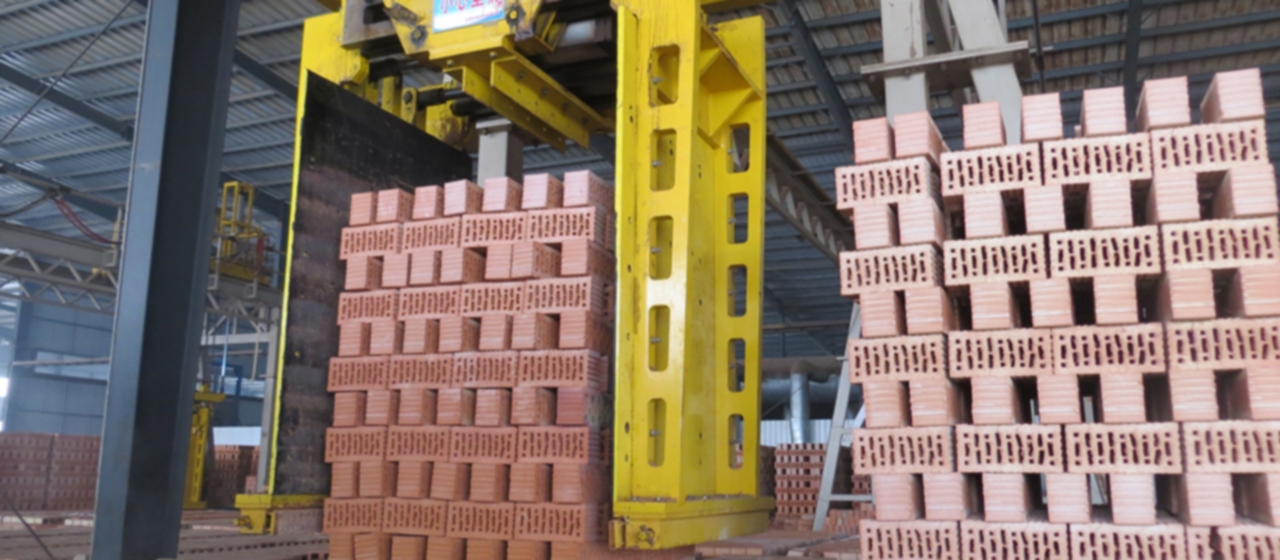
Of course, there are many types of cracks caused by the unreasonable performance and structure of the extrusion equipment, such as the speed problem of the extruder. The clay used in a certain area in Henan has a high plasticity index and significant drying shrinkage. However, after adding coal gangue modification, its drying shrinkage value is still within an acceptable range. The root cause is still the issue with the extrusion equipment. As is well known, modern extruders continuously increase the diameter of the extrusion mud tank, and the pitch of their screw cutters is also increasing. However, as the pitch increases, the rotational speed of the spiral cutter should correspondingly decrease. The diameter of the extruder mud cylinder used by the factory is 500mm, but its spindle speed unexpectedly reaches nearly 50r. p.m; In order to improve the speed of extruding mud strips, the auxiliary blades of the spiral cutter head were also cut to a width of less than 150mm. The extruder head has severe heat generation, which has endangered the quality of the bricks. When a new spiral cutter is replaced (which is also unreasonable), the location and form of the crack change. The cracked bricks or adobe in the photo have a certain regularity in their cracks, which should be a problem with the extrusion equipment. Therefore, when choosing extrusion equipment, especially the “one-time firing” process, one should not only seek cheap prices, but also consider its cost-effectiveness. Choosing an extruder with such a problem will result in greater losses after production. More importantly, it is important to consider the performance of one’s own raw materials and the products produced, adapt to the type of extruder, and “what suits oneself is the best.”.
The above examples are all about solid bricks, because in the past two decades, most extruder manufacturers have mainly focused on the molding of hollow products, while ignoring the extrusion of solid bricks by modern extruders. An extruder that can smoothly extrude hollow bricks may not necessarily be able to extrude good solid brick bodies. Indeed, there is no problem with extruding hollow products in the industry, but there is a problem with extruding solid bricks. It can be seen that different products have different requirements for extruders. As is well known, the middle section of the extruded clay bar generally moves faster, and the core frame of the hollow brick can increase the resistance in the middle, balancing the flow speed of the clay bar section. But when extruding solid bricks, the middle part will be faster and easier to form spiral patterns. If the structure of the spiral cutter head is unreasonable, it is more likely to produce cracks and defects in the billet. Especially in the extrusion molding of decorative bricks, it is necessary to achieve flow velocity balance on the cross-section of the mud bar.
In textbooks of developed Western European countries, the causes of cracks in the billet are also divided into two types: one is caused by extrusion equipment that already exists in the billet; Another reason is the occurrence of the drying process. Therefore, when cracks appear in the billet, the first step is to correctly distinguish the cause, whether it is caused by the equipment or the drying process.
The cracks caused by the extrusion equipment can also be referred to as cracks caused by internal stress in the billet (including core frame cracks). The so-called internal stress cracks are caused by the uneven distribution of extrusion pressure and inconsistent flow velocity of the mud bar section during the forming process of the billet, which forms internal stress inside the billet. During the drying process, cracks appear, and the equipment should be adjusted or modified.